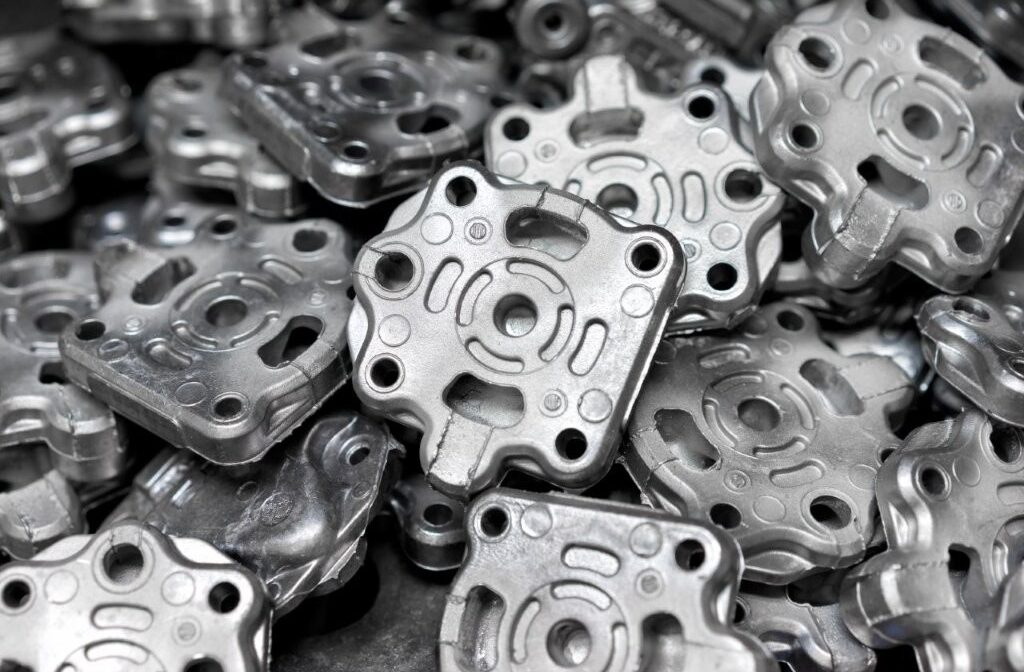
WIE WÄHLEN SIE DIE RICHTIGE LEGIERUNG FÜR IHR GUSSTEILE
Eine gut gewählte Legierung bestimmt die Leistung, Lebensdauer und Zuverlässigkeit Ihres Produkts. Eine falsch gewählte Legierung kann zu unerwarteten technischen Problemen, vorzeitiger Abnutzung oder hohen Wartungs- und Ersatzkosten führen.
Die Herausforderung? Es stehen Tausende von Legierungen zur Verfügung, jede mit ihrer eigenen Zusammensetzung, Eigenschaften und Anwendungsbereich. Von mechanischer Festigkeit über Korrosionsbeständigkeit bis hin zu Gewicht und Bearbeitbarkeit: Das Finden der richtigen Balance erfordert technische Kenntnisse und Einblicke in die spezifische Anwendung. Ein strukturierter Ansatz hilft, Schritt für Schritt zu einer verantwortungsvollen und wohlüberlegten Entscheidung zu gelangen.
DER UNTERSCHIED ZWISCHEN MATERIALIEN UND LEGIERUNGEN
Materialien sind die physischen Stoffe, aus denen Konstruktionen, Komponenten und Produkte hergestellt werden. Eine Legierung ist ein Werkstoff , das aus einer Zusammensetzung von zwei oder mehr Elementen besteht, wobei mindestens eines ein Metall ist. Legierungen sind in der Regel stärker als reines Metall. Durch die Zugabe von Atomen mit unterschiedlichen Größen oder Eigenschaften wird das Verschieben von Atomlagen unter Belastung erschwert. Dies erhöht die Härte und Festigkeit im Vergleich zum Grundmetall.
DIE MEISTVERWENDETEN LEGIERUNGEN
Beim Gießen werden verschiedene Legierungen verwendet, abhängig von den gewünschten Eigenschaften und der Anwendung. Welche Legierungen werden am häufigsten verwendet und welche Anwendungen sind damit verbunden? Nachfolgend finden Sie eine Tabelle, in der die verschiedenen Kategorien von Legierungen, die entsprechenden Typen, die Zusammensetzung der Legierungen und die Anwendung auf einen Blick dargestellt sind.
Kategorie |
Alloy/Typ |
Werkstoffe |
Eigenschaften |
Anwendungen |
Eisenlegierungen | Gusseisen | Eisen, 1,8–4,3% Kohlenstoff, Silizium, Mangan | Gute Gießbarkeit, relativ niedriger Schmelzpunkt, recht stark, spröde, günstig, verschleißfest, vibrationsdämpfend | Maschinenteile, Bau |
Grauguss | Eisen, Kohlenstoff (Graphit in Lamellen), Silizium | Gute Gießbarkeit, gut bearbeitbar, gute Dämpfungsfähigkeit, relativ spröde, gute thermische Leitung | Motorblöcke, Bremsscheiben, Pfannen, Kühler | |
Sphäroguss | Eisen, Kohlenstoff (kugelförmiges Graphit), Silizium, Magnesium | Stärker und zähmer als Grauguss, gute Verschleißfestigkeit, gute Duktilität, gute Bearbeitbarkeit | Kurbelwellen, Pleuelstangen, Zahnräder, Rohre, Ventile | |
Vermikulitguss | Eisen, Kohlenstoff (kompaktes Graphit), Silizium | Gleichgewicht zwischen Grauguss und duktilen Guss, gute Festigkeit, moderate Duktilität, gute thermische Leitfähigkeit | Zylinderköpfe, Zylinderlaufbuchsen, hydraulische Ventile | |
Weißguss (Hartguss) | Eisen, Kohlenstoff (in Zementit), wenig Silizium | Sehr hart, verschleißfest, spröde, schwer bearbeitbar, hohe Druckfestigkeit | Verschleißfeste Teile, Beschichtungen, Bruchplatten. | |
Schwarzguss (Temperguss) | Eisen, Kohlenstoff (ausgeglüht), Silizium, Mangan | Stark, zäh, gute Bearbeitbarkeit, moderate Verschleißfestigkeit, weniger spröde als Weißguss | Rohrverbindungen, Niederdruckventile, komplexe Maschinenteile. | |
ADI | Eisen, Kohlenstoff, Nickel, Molybdän, Magnesium | Sehr hohe Festigkeit, gute Zähigkeit, verschleißfest, gut bearbeitbar nach Wärmebehandlung | Zahnräder, Achsen, Aufhängungsteile, schwere Maschinenteile. | |
SIMO | Eisen, hochsilizium, Molybdän | Sehr korrosionsbeständig, hohe Verschleißfestigkeit, hitzebeständig, schwer bearbeitbar | Ventile, Pumpen, Teile in der chemischen Industrie. | |
Nicht-Eisenlegierungen | AlSi10Mg | Aluminium, 10% Silizium, Magnesium | Leichtgewicht, gute Festigkeit, korrosionsbeständig, gut bearbeitbar, geeignet für 3D-Druck, schweißbar. | Automobilteile, Luftfahrt, 3D-gedruckte Komponenten |
AlSi12 | Aluminium, 12% Silizium | Gute Gießbarkeit, leicht, gute Korrosionsbeständigkeit, gute Festigkeit bei niedrigen Temperaturen | Gehäuse, Getriebeteile | |
AlMg5 | Aluminium, 5% Magnesium | Leichtgewicht, gute Korrosionsbeständigkeit (Salzwasser), gute Schweißbarkeit, mäßig stark | Schiffbau, Transport | |
AlZn5Mg | Aluminium, 5% Zink, Magnesium | Leichtgewicht, hohe Festigkeit, gute Korrosionsbeständigkeit, geeignet für Konstruktionen mit hoher Belastung | Luftfahrt, Sportausrüstung | |
AlSi7Mg0,3/0,6 | Aluminium, 7% Silizium, 0,3–0,6% Magnesium | Leichtgewicht, gute Gießbarkeit, gute Korrosionsbeständigkeit, gute Festigkeit und Zähigkeit | Automobilteile, Maschinenteile | |
Bronze | Ca. 90% Kupfer, 10% Zinn (manchmal Aluminium, Mangan) | Stark, verschleißfest, gute Korrosionsbeständigkeit, gute Bearbeitbarkeit, gute Dämpfungsfähigkeit | Gleitlager, Kunstobjekte, Zahnräder, Pumpen, Schiffspropeller, Elektro | |
Aluminiumbronze | Kupfer, 5–12% Aluminium | Sehr korrosionsbeständig, verschleißfest, stark, gut bearbeitbar | Ventile, Pumpenteile, maritime Anwendungen | |
Manganbronze | Kupfer, 1–4% Mangan | Gute Korrosionsbeständigkeit, hohe Verschleißfestigkeit, gute Federkräfte | Gleitlager, elektrische Kontakte, Federkontakte, Pumpenteile | |
Messing | Kupfer, 5–45% Zink | Gute Bearbeitbarkeit, gute Korrosionsbeständigkeit, gute elektrische und thermische Leitfähigkeit | Fittings, Ventile, Musikinstrumente, Dekoration, elektrische Komponenten | |
Zinklegierungen | Zink, oft Aluminium, Magnesium, Kupfer | Gute Gießbarkeit, günstig, leicht, moderate Festigkeit, gute Korrosionsbeständigkeit | Gussarbeiten, Schlösser, Handgriffe, Auto-Teile | |
Edelstahllegierungen | Edelstahl 316 | Eisen, 16–18% Chrom, 10–14% Nickel, 2–3% Molybdän | Sehr gute Korrosionsbeständigkeit, stark, gut schweißbar, beständig gegen Salzwasser und Chemikalien | Chemische Industrie, medizinische Geräte, maritime Anwendungen |
Duplex | Eisen, 18–28% Chrom, 4,5–8% Nickel, 0,05–5% Molybdän | Sehr gute Korrosionsbeständigkeit, hohe Festigkeit, gute Schweißbarkeit, beständig gegen Spannungsrisskorrosion | Offshore, chemische Industrie, Brücken, Lagertanks | |
Super Duplex | Eisen, 24–26% Chrom, 6–8% Nickel, 3–5% Molybdän | Ausgezeichnete Korrosionsbeständigkeit, sehr hohe Festigkeit, beständig gegen schwere chemische und maritime Bedingungen | Salzwasseranlagen, Öl- und Gasindustrie, chemische Verarbeitung | |
Hastelloy | Nickel, 14–22% Molybdän, 14–22% Chrom | Außergewöhnlich korrosionsbeständig, hitzebeständig, stark, schwer bearbeitbar | Chemische Verarbeitung, Luft- und Raumfahrt, Kraftwerke | |
Monel | Ca. 65% Nickel, 30% Kupfer, Rest Eisen und Mangan | Sehr korrosionsbeständig, stark, hitzebeständig, gute Bearbeitbarkeit, beständig gegen Salzwasser und Chemikalien | Pumpen- und Ventilteile, maritime Anwendungen, chemische Industrie | |
Inconel | Nickel, Chrom, Eisen | Ausgezeichnete Hitzebeständigkeit, sehr stark, sehr korrosionsbeständig, schwer bearbeitbar | Turbinenblätter, Auslassventile, Wärmetauscher, Luftfahrt | |
Sonstige legierungen | Nickellegierungen | Nickel, oft mit Zugabe von Chrom, Eisen, Molybdän | Hitzebeständig, sehr korrosionsbeständig, stark, schwer bearbeitbar | Gasturbinen, chemische Industrie, hitzebeständige Teile |
Kupferlegierungen | Kupfer oft mit Zugabe von Nickel, Silizium, Beryllium | Gute elektrische und thermische Leitfähigkeit, korrosionsbeständig, stark, gut bearbeitbar | Elektrische Leiter, Wärmetauscher, Münzen, Rohre | |
Titanlegierungen | Titan, oft mit Zugabe von Aluminium, Vanadium | Leichtgewicht, sehr stark, sehr korrosionsbeständig, biokompatibel, schwer bearbeitbar | Luftfahrt, medizinische Implantate, Sportausrüstung, chemische Industrie | |
Kobaltlegierungen | Kobalt, Chrom, Molybdän, Nickel | Sehr hitzebeständig, sehr verschleißfest, biokompatibel, schwer bearbeitbar | Medizinische Implantate, Zahnmedizin, Schneidwerkzeuge, Turbinen |
SCHRITT-FÜR-SCHRITT-PLAN ZUR RICHTIGEN ENTSCHEIDUNG
Um die richtige Legierung für Ihr Gussprojekt auszuwählen, ist es wichtig, zunächst die Anforderungen und gewünschten Eigenschaften des Endprodukts klar zu definieren. Hier ist ein Schritt-für-Schritt-Plan, der Ihnen hilft, zu dieser Wahl zu gelangen:
1. BESTIMMEN SIE DIE WICHTIGSTEN MATERIALEIGENSCHAFTEN
Bei der Auswahl einer Legierung ist es entscheidend, die wesentlichen Eigenschaften für Ihre Anwendung oder Ihr Produkt zu bestimmen. Priorisieren Sie die Eigenschaften, die für die Funktion des Bauteils in seiner Umgebung am bedeutsamsten sind. Stellen Sie eine Hierarchie der Anforderungen auf (z. B.: zunächst Festigkeit, dann Korrosionsbeständigkeit, danach Bearbeitbarkeit).
- Mechanische Festigkeit: wichtig, wenn das Bauteil schweren Belastungen standhalten oder strukturell eingesetzt werden muss.
- Korrosionsbeständigkeit: wesentlich, wenn das Produkt Feuchtigkeit, Chemikalien, Salz oder anderen korrosiven Umgebungen ausgesetzt ist.
- Hitzebeständigkeit: von Bedeutung für Bauteile, die hohen Temperaturen standhalten müssen, wie beispielsweise Motorenteile.
- Verschleißfestigkeit: relevant für Bauteile, die Reibung oder Abnutzung ausgesetzt sind.
- Verformbarkeit und Duktilität: wichtig bei komplexen Formen oder dünnwandigen Bauteilen.
- Schweißbarkeit und Bearbeitbarkeit: entscheidend, wenn das Bauteil verschweißt, gebohrt oder bearbeitet werden muss.
- Oberflächenqualität: wichtig bei sichtbaren Bauteilen oder wenn eine weitere Oberflächenbehandlung erforderlich ist.
- Gewicht: leichte Legierungen sind wünschenswert bei Anwendungen, bei denen das Gewicht eine Rolle spielt, wie im Transport oder in der Luftfahrt.
2. DEFINIEREN SIE DEN PRODUKTIONSPROZESS
Bestimmen Sie zunächst den Produktionsprozess, der für Ihr Gussprojekt geeignet ist. Es stehen verschiedene Gusstechniken zur Verfügung, wie beispielsweise Druckguss, Kokillenguss, Sandguss oder Feinguss. Aspekte wie die Größe der Produktionsserie, Produktionszeit, lineare und geometrische Genauigkeit, Oberflächenqualität, Wanddicke und die Komplexität des Produkts oder Bauteils bestimmen den richtigen Gussprozess.
3. BERÜCKSICHTIGEN SIE SEKUNDÄRVERARBEITUNG UND OBERFLÄCHENBEHANDLUNG
Der nächste Schritt, um zur richtigen Legierung zu gelangen, besteht darin, zu prüfen, ob und welche Prozesse nach der Primärproduktion stattfinden müssen. Muss das Produkt beispielsweise geschweißt, montiert oder weiter bearbeitet werden? Oder ist eine spezifische Oberflächenbehandlung oder ein bestimmtes Erscheinungsbild gewünscht (zum Beispiel anodisieren)?
4. KONSULTIEREN SIE EXPERTEN ODER DATENBANKEN
Sobald die funktionalen und wirtschaftlichen Anforderungen klar sind, empfiehlt es sich, Materialdaten über technische Datenbanken, Normen oder spezifische Werkzeuge wie Alu-Key (für Aluminiumlegierungen) zu vergleichen. Mit diesen Quellen können Sie schnell und objektiv Eigenschaften, Anwendungsbereiche und Alternativen gegenüberstellen. Noch effektiver ist es, einen Materialspezialisten oder Ingenieur hinzuzuziehen, der Erfahrung mit Ihrer speziellen Anwendung hat. Bei ELCEE bieten wir diese Unterstützung aktiv an – sowohl aus der Ferne als auch vor Ort – damit Sie mit Sicherheit die am besten geeignete Legierung auswählen.
DIE RICHTIGE LEGIERUNG FÜR IHR PROJEKT
Die Leistung, Lebensdauer und Kosteneffizienz technischer Produkte werden stark von der gewählten Legierung beeinflusst. Möchten Sie mehr technisches Wissen erwerben, das Sie für verschiedene Projekte nutzen können? Melden Sie sich zu einem Training an der ELCEE Academy an. Hier bieten wir Schulungen zur Materialauswahl, Produktionstechniken und Designoptimierung an.
Benötigen Sie einen Sparringspartner, um die technischen Details Ihres Projekts zu besprechen? Zögern Sie nicht, uns zu kontaktieren. Unsere Experten kommen gerne zu Ihnen, um Ihre spezifische Anwendung zu besprechen und direktes Feedback zu geben.